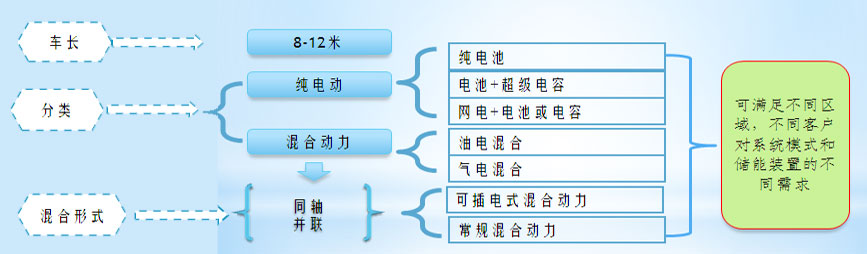
公司经过近10年的潜心研发,建立了基于自主化的多档AMT自动变速箱与驱动电机高效集成的同轴并联混合动力机电耦合驱动系统平台,研发了16代混合动力客车、5代纯电动以及3代插电式混合动力客车,产品涵盖了8米到12米,可满足不同区域,不同客户对系统模式和储能装置的不同需求。
插电式混合动力客车
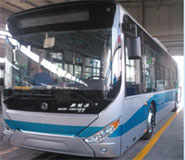 |
  |
  |
  |
2010年在常规混合动力系统的基础上,中通客车又研发了插电式同轴并联混合动力客车,在2013年开始批量推向市场,该车型在继承原有系统高可靠性、高安全性的基础上,加大纯电动续驶里程,进一步提高整车的节油效果。针对基础设施建设较为完备的区域,可以实现车辆的外接充电,加大纯电动运营里程,减少污染物排放,降低燃料消耗,而对于没有条件的地区也可以作为常规混合动力客车正常运营。
中通同轴并联插电式混合动力客车在混合动力工况下节油率达到40%以上,插电工况下综合节油率达到60%以上,节能效果明显,产品可靠性、安全性得到验证。
|
核心技术
动力电池系统:电池容量从16Ah提高到60-80Ah。满足整车纯电动续驶里程的同时,延长电池使用寿命,加大整车制动能量回收比例。
驱动电机系统:将普通混合力用的45Kw、420N.m永磁同步电机提升到65Kw、600N.m,提高电机系统的散热效果,增加纯电动模式的动力性能。
电动助力转向系统:采用常流式电动液压转向系统,其平均运行功率只有310W,有效节能75%以上。为实现发动机的怠速和低速熄火,提供必要的技术条件。
充电系统方案:可选用手动充电和自动充电两种模式,满足国家标准。可以实现车载充电、独立充电机、充电桩等多种充电模式。
智能空调系统:根据电池电量、发动机状态,由整车控制器通过仪表实现空调系统的智能控制,实现整车热环境的最优化控制,提高空调能耗比。
中通纯电动客车产品
纯电动客车动力系统采用目前应用最为广泛,状态最为稳定的电动机直驱形式,根据不同区域的基础设施建设情况,研发了电池快换式、整车充电式,网电耦合在线充电式等多种充电模式,产品覆盖了团体、公交、旅游等多功能用途。
性能优势
安全性: ① 建立设计标准:制定了适用于新能源车辆的高低压电器安全设计标准,并应用在实际开发工作中;引入安全失效模式与潜在后果分析设计方法,消除新能源车辆设计安全性风险,在设计入口进一步降低车辆安全隐患问题的输入;
②提高主动安全性:高压电池箱配置烟雾报警、自动灭火、碰撞惯性断电等安全结构设计,提升主动安全设计等级;
③安全实验验证:对新结构、新材料、新工艺进行安全验证,修正设计方向,消灭安全隐患。
可靠性:高度集成的低压和高压配电控制装置;冗余保险主动安全与被动安全集成设计;分层和模块化控制的整车网络系统架构;完善的充电软硬件措施;智能远程监控系统平台,实现整车全生命周期的可靠性管理。
节能性: ①轻量化技术:在小矩形管全承载技术的基础上,深度挖掘车身轻量化技术,通过优化结构或选用新材料,降低整车质量。在车身骨架及蒙皮、地板、镁合金风道及内饰件和附件、司机隔栏、采用薄铝板封舱、轻质高效空调、铝合金轮辋、减小玻璃尺寸、优化电器附件去除多余线束、去除不必要的附属品等方面,实现整车轻量化。
②多能源智能管理技术:通过对整车电池、电机、发动机、电动助力、空调等各关键零部件的智能控制,优化整车能量分配策略,提高整车能源转化效率,提高整车节油效果。
新能源客车市场运营效果
新能源客车市场概况:
新能源客车市场分布:
截至目前,中通新能源客车累计大规模运营数量已近5000辆,总里程超过6亿公里。分布在山东大部分城市、河南濮阳、内蒙古集宁、天津、杭州、福州、广州、海口、新加坡、菲律宾等70余个国内外城市。
新能源客车市场能耗情况:
插电混合动力客车:目前,在城市公交工况下,中通油-电混合动力客车节油率分布在25.2%~32.4%之间。插电式混合动力系统综合节油率达到50%以上。
纯电动客车:标准城市工况下,中通12米纯电动客车每公里耗电不到1度电,10米纯电动客车每公里耗电0.7度左右。城市公交工况下,以12米纯电动公交车节能减排数据如下:
市场运营效果:
常规同轴并联混合动力系统客车 在过去几年占有重要地位,极大地满足了客户的节能性需要,更重要的是解决了混联系统在可靠性方面不足的技术难题,获得了客户的认可。
针对2013年大批量推广的插电式混合动力客车,经过众多市场的验证已经成熟,产品的可靠性高、节油率高,其原因在于充分借鉴了常规混合动力的技术优势,重点发挥了大电池、大电机、深度发动机停机、高精度驾驶员意图识别等技术优势,获得了圆满的成功。
针对某些区域不适合插电的情况,我公司适当调整控制策略,使非插电模式下的插电式混合动力客车整车综合节能率远远超过常规混合动力客车。